Integrated In-House Production
Our integrated production system covers everything from material procurement to cutting, heat treatment, grinding, and assembly & pressure adjustment.
High-quality production is also possible at our Vietnam plants, which use the same materials and processing equipment as our facilities in Japan.
We will continue striving to build bonds of trust with our customers through the use of our smooth and reliable production systems.
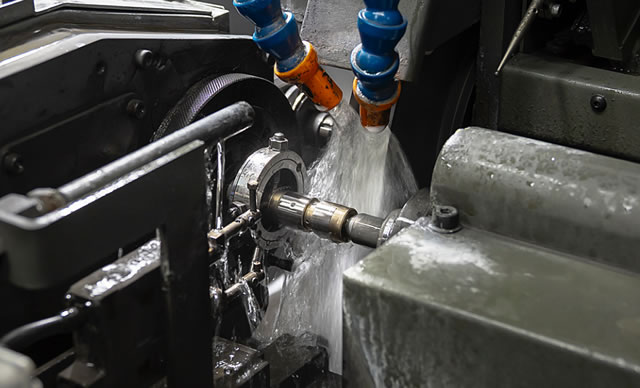
Materials that are Difficult to Machine, Shape, and Process
By using our accumulated know-how and sophisticated technologies, we have realized micron-level precision processing technology for materials that are difficult to work with. In particular, we have created parts that are expected to be of great quality and are rated very highly by our customers, such as the mass production and processing of fuel injection nozzle parts for diesel engines for marine and land vehicles.
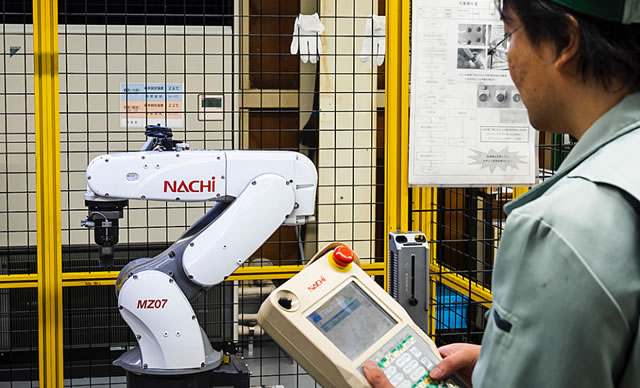
Deburring Technology
Most of the parts that we offer are essential safety parts. Even the smallest burrs are not acceptable on parts used for automobiles, construction equipment, or diesel engines for marine and land vehicles. We independently manufacture a variety of machines and devices, and we do so with great efficiency. Among these, our deburring machines that efficiently employ electrolysis and brushes provide a great contribution to the production of burr-free parts.
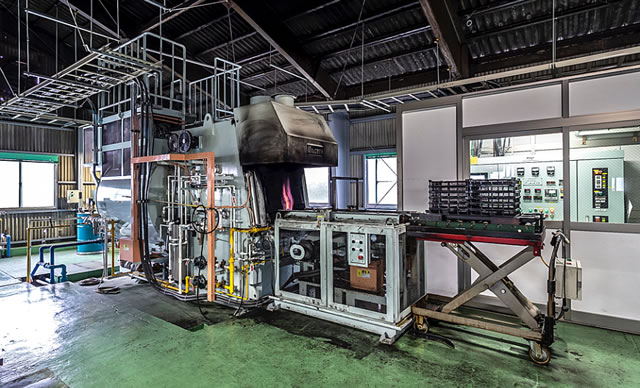
Heat Treatment Technology
Most metal parts used in high-pressure and other such strenuous settings have been heat-treated. We own a drip-feed gas carburizing furnace as well as other equipment including a tempering furnace, sub-zero treatment device, various types of durometers, and metallographic microscopes, which allow us to perform heat treatment in-house with speed and efficiency. We also pay close attention to equipment management and quality control and have received heat treatment certification (for quenching, carburizing quenching, and carbonitriding quenching) from major construction equipment manufacturers.
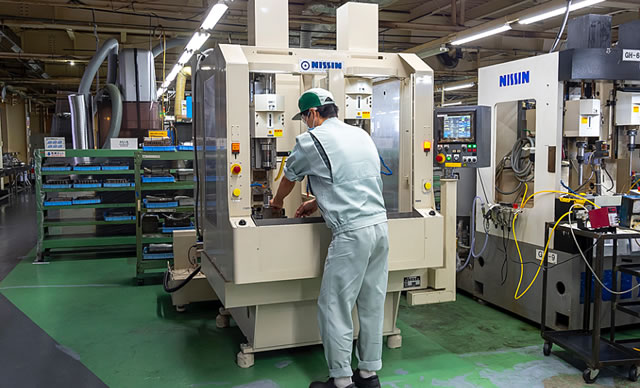
Minute Clearance Processing
We continue to face the challenges of ever-increasing precision requirements of mechanical industrial products for improved control accuracy and reduced energy loss. Our engineers have a wealth of knowledge and experiences as well as the latest grinding equipment, tools, inner and outer diameter processing technology and precision measurement technology at their disposal, with which we pursue the improvement of minute clearance accuracy down to micrometer level.
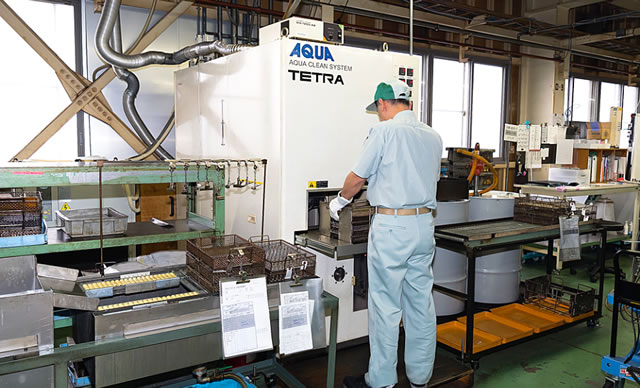
Anti-Contami Measures
Production of high-quality hydraulic equipment requires a clean environment where foreign matter cannot enter and an efficient production line. We use parts washers that have been designed and developed in-house that prevent foreign matter from entering. In addition, all parts are cleaned using demagnetization treatment and a hydrocarbon cleaning machine (with ultrasonic and vacuum drying), and as shipped in a clean state according to customers’ contami standards.※What is contami?
“Contami” is a term that comes from “contamination” and “contaminant”, and refers to things that adversely affect hydraulic systems or the state of being contaminated with such substances. This primarily refers to minute solid particles such as chips, fibers, various types of oil, and water.
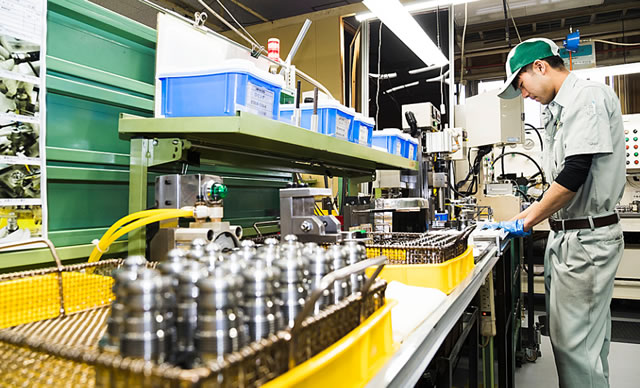
Relief Valve Assemblies
Relief valve assemblies are used in things such as the hydraulic devices of construction equipment. We carry out integrated production of these from parts processing to assembly and pressure adjustment. Since these products have very strict foreign substance standards, we use a one-piece flow assembly line that is overseen by experienced technicians. An inspection device group created by TOWA JAPAN, active both in Japan and overseas, performs pass/fail judgment of products based on pressure settings and numerical measurements.
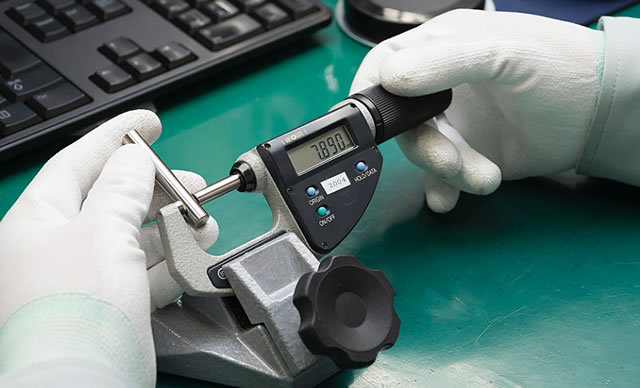
Inspection via Precision Measurement
Accurate product measurement and data analysis are required to maintain the reliable production and supply of precision machined parts. We strive for reliable precision measurement by keeping the temperature of the measurement room at 23 ± 2℃, maintaining strict and thorough control of the room and product temperature before measurement. We have a wide array of measuring devices at our disposal, including devices for measuring roundness and cylindricity, shape, roughness, and coordinate measuring machines, allowing us to maintain thorough product quality control.